Medical Device Burst and Leak Testing – Wet or Dry?
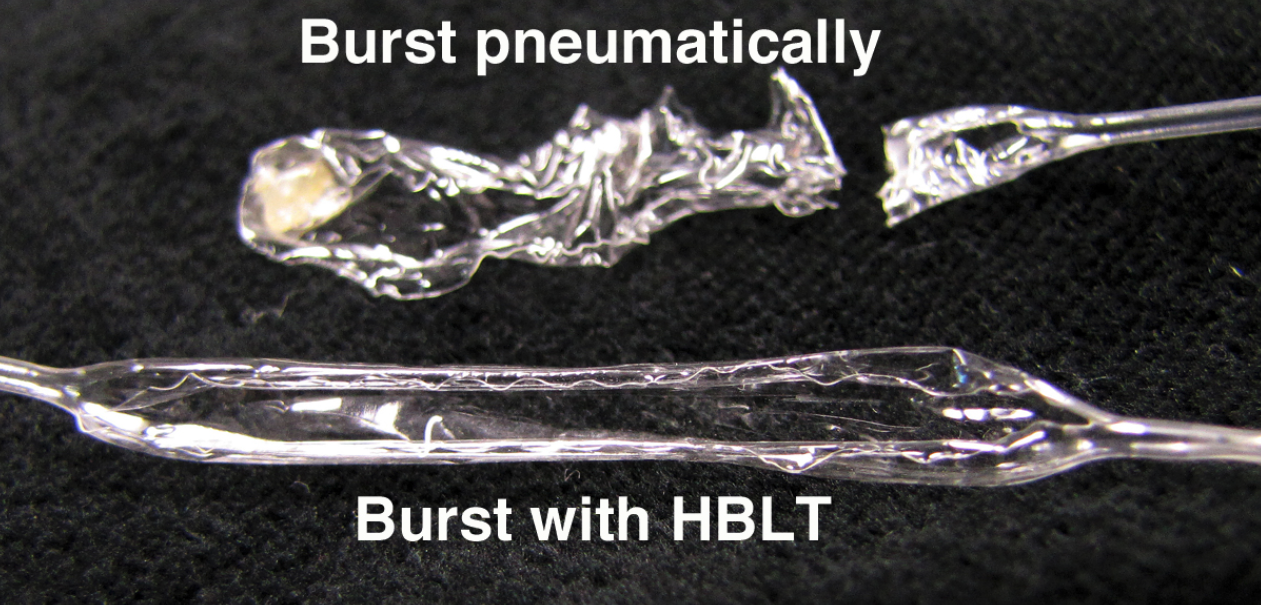
Medical Device Burst and Leak Testing
Get Wet or Keep Dry?
Medical devices are required to be tested for leaks or imperfections, and many OEMs are unsure as to what is the best medium for testing—air or water? The two modalities are not equivalent, and although testing with water might appear to be more expensive, it can lower testing costs in many applications. Particularly when testing medical devices that handle liquids, testing with water may lower validation costs which are time consuming, and require additional testing, to show that gas tests will yield results that predict actual field behavior. Airplane designs are tested in wind tunnels and boats are tested in the water. Devices that operate in and deliver liquids should be tested with liquid.
Liquid cons:
A downside to testing with water is that it may contaminate the product. If this is unacceptable, AQL (Acceptable Quality Level) testing is often used. When using AQL testing, a small percentage of a given lot of the product is tested and if the results all fall within a statistically acceptable range, the rest of that lot passes.
Liquid pros:
No adiabatic heating –
Normally when pressure testing with gas, it is necessary to allow a “settling” time when the test part is first pressurized. As the gas is admitted to the part it is compressed, which increases its temperature. If a time/pressure decay test is started without settling time, the gas will cool, the pressure will drop, and a false burst or leak may be reported. When a failure is detected on a medical device the root case must be determined and explained. A false event (burst or leak) can cause unnecessary work and delay the release of product for sale. Adiabatic heating does not occur with liquid testing because the liquid is incompressible.
High sensitivity –
Very small changes in test volume result in large changes in pressure because water is incompressible. Because of this and no need for settling time, it is possible to detect tiny leaks faster and increase testing throughput.
Realistic test results –
Pressure testing of a device is done to verify the strength of its components, its connections and its seals, and to identify weak points that result in distensions, bursts or leaks. When testing is done with water using a hydraulic instrument that does not store energy (unlike an air-over-water or pneumatic system), the failure results will be representative of actual failures in the field. It is often difficult to correlate the results of tests done with gas versus tests done with liquid. The benefits of testing in conditions that closely replicate the real world are obvious.
The photograph above shows two balloons that have burst at the same pressure. The upper balloon was burst with compressed gas. The failure triggered the sudden exhaust of compressed gas that tore the balloon into multiple pieces, leaving little hope of analyzing the origin point of the failure. In the final analysis, you know that the product DID fail, but not where or why it failed, so it’s a challenge to make design changes to remedy the problem.
The lower balloon failed under water pressure. Once the fissure formed at the point of failure, a minute amount of water escaped, causing the pressure to drop to zero almost instantaneously, leaving the rest of the balloon intact – exactly as it would fail in actual use.
Continue reading and Download the full white paper to learn more about the costs, safety, flow testing and overall testing summary at https://crescentdesign.com/hblt/.