Vertical Lamination Temperature Stability & Repeatability
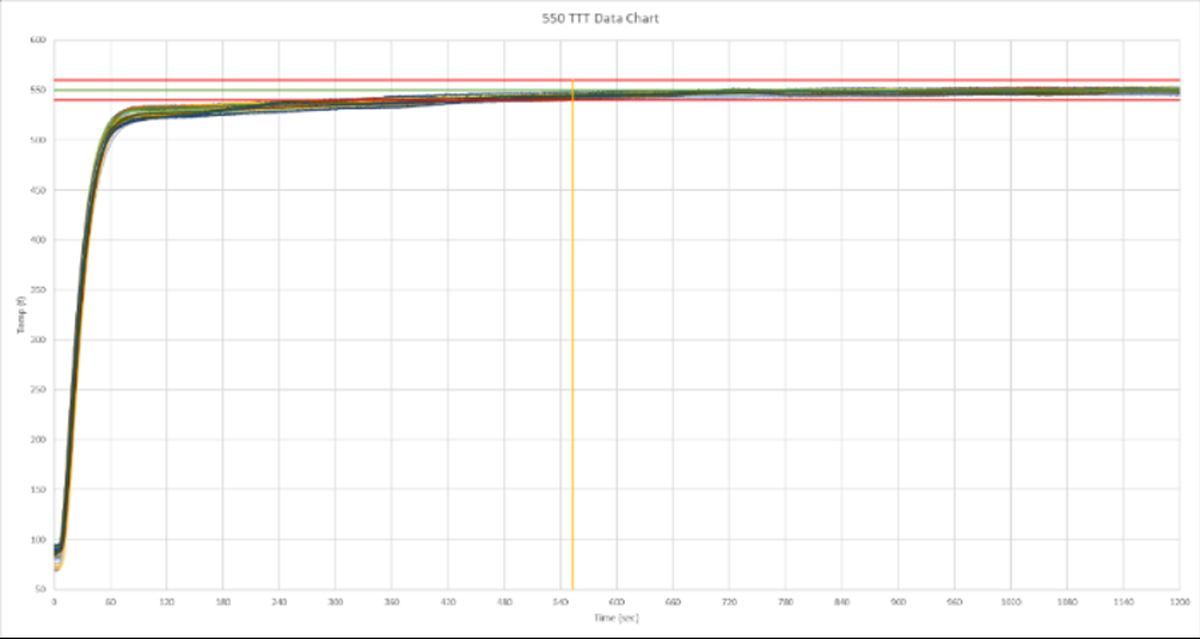
Rudimentary and legacy market heating methods with larger windows of variability have been accepted to accomplish basic lamination needs for catheter manufacturing. As the industry grows, material and designs become more complex, along with increased requirements for process and equipment validation, higher precision controls are required. In response to the industry demand for tighter temperature control, airflow, run to run repeatability and lane to lane uniformity, Machine Solutions Inc. has released the Vertical Laminator product line. The Vertical Laminator line (VL400 – 4 lane and VL1000 – 10 lane) have been designed to be operator-friendly machines that hold consistent temperature, airflow and rate of processing output. Key design focus areas: single part heater nozzles, in-line digital flow meters, minimal foot print to maximize floor space, and State of the art control systems.
Design Solutions:
MSI’s VL product line design focuses on the following key areas to fill the increased market need and allow for optimal control and repeatable processing.
- Single part heater nozzle: Creating an air tight part to minimize thermal and airflow loss.
- In-line digital flow meters: The addition of in line digital airflow meters yield accurate flow rate measurements and enables the user more precise control and repeatability in setting machine parameters (HMI controlled airflow is also available)
- Industry standard PC based control system: Gives the user more control over the lamination process, higher safety standards, and ability to save multiple processing parameters and product/process recipes.
- Temperature standard fixture (optional; image right): is designed to allow unobstructed air flow while holding the thermocouple in the center most point of the nozzle to accurately record the temperature where product would experience heat.
Problem Statement:
In the lamination market, machine to machine inconsistency leads to non-uniform process results and excessive scrap rates. In some machine bases, lane to lane uniformity and run to run repeatability has led to damaged product and excessive hours of wasted time attempting to validate unreliable equipment.
Test Methods Selection:
TTT (Time to Temp) test method was developed by MSI to record consistency of;
- Temperature rate of climb over time
- Temperature rate of climb in degrees
Process Simulation Test Method (Processing) was developed by MSI to record consistency of temperature once the VL had achieved its process ready state. Observations include;
- Lane to Lane consistency
- Run to Run consistency
Test Methods Explanation:
On a system calibrated per manufacturers recommendations: A test run consisted of running 1 machine with all 4 lanes simultaneously and performing a Time to Temperature Test (TTT) run followed by a Processing Temperature (Processing) Test run. These tests were completed on a total of 3 machines independently. Then the machine cooled back to the heater off/ambient air condition (defined as between: 65-100˚f) prior to starting the next test run.
Time to Temperature (TTT): (550˚F, 130SCFH) From the manual screen, the test operator setup the VL400 so that the gripper rack was disconnected, and the heater rack was set to a reachable height around 1.5m. Then the test operator attached the temp probe fixture’s to each of the four lanes and the data collector. After insuring the appropriate parameters input to the machine the test operator started recording on the data collector then turned on heating for each lane of the VL400. The data collector remained active for at least 20 minutes. After the data collector was switched off the heater rack was moved to the home position and heat and air flow remained on.
Processing Temperature Test (Processing): (550°F, 130SCFH, 10mm/sec) After the Time to Temperature (TTT) test run was performed, the test operator initiated the data collector, set a move distance on the manual screen to move the heater rack from the start/top position to end/bottom position (1750mm), Dwell for 10 seconds, then move back from the end/bottom position to the start/top position (-1750mm) for a total move of 3500mm while continually heating at the set temperature and flow.
Results:
Time to Temperature (TTT): Testing confirmed that the Vertical Laminator (VL) product line held to ±3˚F. Mapping the heat signature of the 3 machines shows a repeatable ramp up across all 4 lanes and all 3 machines. This superior lane to lane uniformity and run to run repeatability will reduce validation time and scrapped product. This test also confirms the time for temperature tolerance stability at 9:22min secs from start up. This reinforces the 10min heat up time and heaters always on run configuration Machine Solutions recommends.
Figure 1: Time to Temperature Test Combined Data Chart
Processing Simulation: testing shows that after tempurature stabilization, the temperature measured at center of nozzle, where the product is processed, is consistent and repeatable during a simulated processing run, reinforcing superior lane to lane uniformity and run to run repeatability.
Table 1 Processing Simulation Statistical Analysis
Processing Simulation Statistical Analysis | |||
Maximum | 552.93 | Set Point | 550 |
Minimum | 545.23 | Highest Above Setpoint | 2.93 |
Average | 549.54 | Lowest Below Setpoint | -4.77 |
Standard Deviation | 1.335 |
Figure 2 Processing Simulation Combined Data Chart
LEARN MORE ABOUT OUR LAMINATION EQUIPMENT HERE
[/vc_column_text][/vc_column][/vc_row]